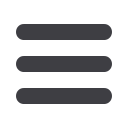
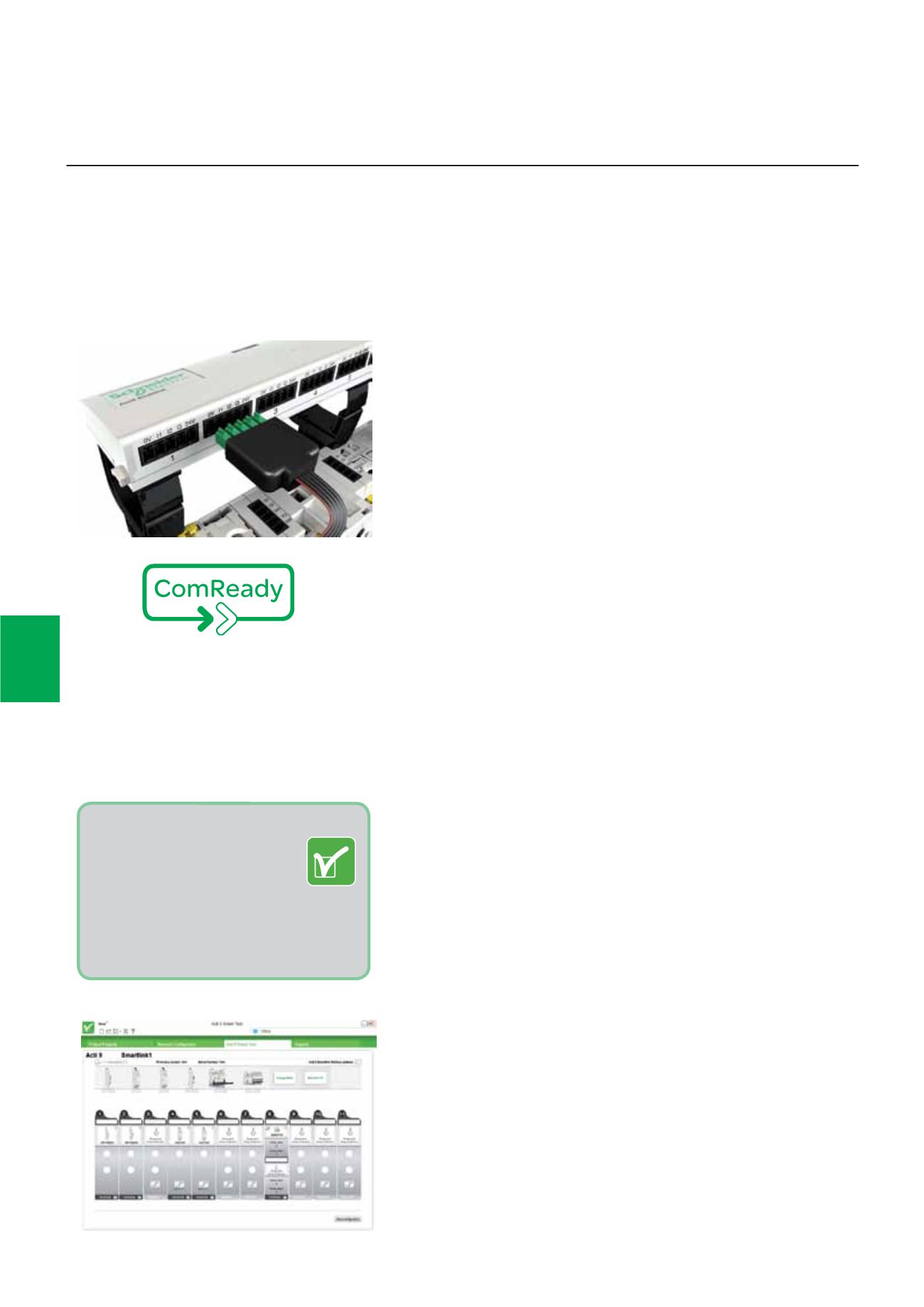
6/16
6
Acti 9 smartlink
Control, remote control,
indication
IEC/EN 61131-2
Acti 9 Smartlink Modbus Slave and Acti 9 Smartlink Ethernet are used to transfer
data from Acti 9 devices to a PLC or monitoring system via the communication
system:
b
b
Modbus serial line for Acti 9 Smartlink Modbus Slave
b
b
Modbus Ethernet TCP/IP or http for Acti 9 Smartlink Ethernet.
Functions
Data transmission between the network and Acti 9 devices
b
b
Circuit breakers, residual current circuit breakers, residual current devices:
v
v
open/closed state
v
v
tripped state
v
v
number of opening/closing cycles
v
v
number of tripping actions.
b
b
Contactors, impulse relays:
v
v
opening control
v
v
closing control
v
v
open/closed state
v
v
number of opening/closing cycles
v
v
total period of operation of the load (device closed).
b
b
Remote controlled circuit breaker/Reflex iC60:
v
v
opening control
v
v
closing control
v
v
open/closed state
v
v
tripped state
v
v
number of opening/closing cycles
v
v
total period of operation of the load.
b
b
Power meters:
v
v
number of pulses recorded
v
v
pulse value setting (e.g. kWh)
v
v
total consumption recorded
v
v
estimate of power consumption.
b
b
Analog sensors only for Acti 9 Smartlink Ethernet:
v
v
temperature sensor
v
v
humidity sensor,
v
v
CO
2
detector,
v
v
optical detector
v
v
...
All the data are stored in memory: number of cycles, consumption, period of
operation, even in the event of a power failure.
Acti 9 Smartlink can also exchange data with any device having 24 V DC digital
inputs/outputs.
No configuration of the connected products is required.
When Acti 9 Smartlink is switched on, communication automatically adjusts to the
Modbus Master or Ethernet (PLC, control station) communication parameters.
Installation
b
b
Mounting in switchboards:
v
v
width 24 modules per row
v
v
minimum spacing between rails 150 mm.
b
b
Mounting on
v
v
DIN rail, with
mounting kit
A9XMFA04
v
v
Linergy FM 80 A, with
locking clips supplied
v
v
Linergy FM 200 A, wtih
mounting kit
A9XM2B04.
Test
b
b
The communication and cabling test for the connected devices can be performed
using Acti 9 Smart Test software
Acti 9 Smart Test software
b
b
Electrical continuity test
b
b
Functional testing of the devices
b
b
Report printing
b
b
Printing of a simplified diagram
b
b
Project archiving
b
b
Compatible with Windows XP, Windows 7,
Windows 8
b
b
To be download on: Schneider Electric web sites:
v
v
schneider-electric.comor
v
v
schneider-electric country web site
PB107797-47
DB404502
DB405140
DB406513